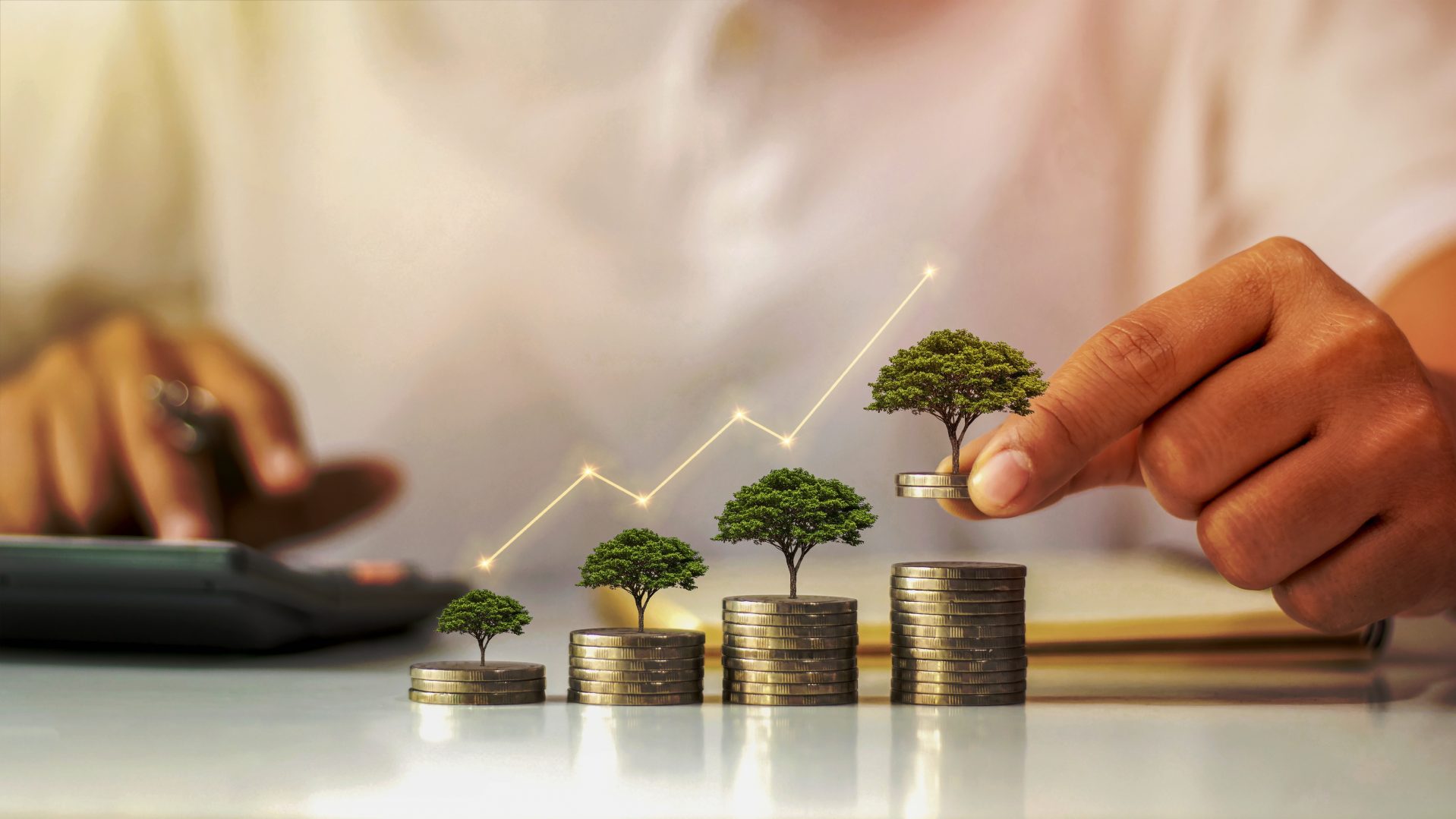
Dutch Energy Saving Obligation
➔ Companies and institutions with an energy consumption of 50,000 kWh of electricity or 25,000 m3 are subject to the new Dutch Energy Saving Obligation.
Great ideas for Mandatory Energy Savings in The Netherlands as of July 1st 2023
Helping to save the planet by saving energy will no longer be optional, but mandatory for many industrial companies in the Netherlands from July 1, 2023. For some, this may sound complicated or like an extra burden in already extremely complicated times. Questions arise such as “Where will I find the time to implement this?” or “How do I know that my environmentally sustainable investments are also financially sustainable?” Let’s take a look at what solutions are on the horizon for (non-)mandatory energy savings in industrial plants. And what is the Best Practice, at the lowest possible Total Cost of Ownership (TCO) possible?
➔ Companies and institutions with an energy consumption of 50,000 kWh of electricity or 25,000 m3 are subject to the new Dutch Energy Saving Obligation.
If your company is subject to this requirement, you may be on a complex and time-consuming path. But by looking at the details, rather than the big picture of energy savings opportunities, you may be able to move forward sooner, faster, and cheaper than you think.
There are a number of steps you need to take if the Energy Saving Obligation applies to your situation:
Step 1:
Implement all measures with a payback period of 5 years or less.
Step 2:
Implement all applicable measures from the approved Energy Conservation Measure Lists (EMLs).
Sometimes, a small change can make a big difference—some great examples
Don’t get completely overwhelmed with solutions that are either too complicated, too time-consuming, or too expensive, let us introduce you to a very smart, proven, and reliable way to save on energy costs: magnetic Non-Contact Drives.
Before we try to convince you of a solution that almost seems too good to be true (it isn’t), let our customers show you their results:
Tata steel
– Investment : OPEX Budget
– Solution : Non-Contact Drives for 4 Pumps of each 75 kW
– Energy saving : Equivalent to 360 households’ annual energy consumption
Indorama
– Investment : OPEX Budget
– Solution : 160kW radial fan
– Return period : 0,5 year
– Saving : Reduction of the total carbon footprint and maintenance
VPR
– Investment : OPEX-budget
– Return period : 5 months based on energy savings alone
– Energy saving : Equivalent to 1.000 households’ annual energy consumption
How does this work?
If you think about it, the essence of all production revolves around transporting materials from one place to another. The most commonly used are liquids (such as water, oil, chemicals, etc.) and gases (such as air, oxygen, etc.). Air and liquids are also needed to cool production processes. Rotating equipment such as pumps and fans are needed to move liquids and air. Up to 65% of the electrical energy used in industry is consumed by rotating equipment (source: IEA).
And if we zoom in on the pumps used to transfer liquids, around 25%, and in some industries, as much as 50%, of the electrical energy is spent on pumping systems. So it is precisely these parts of the installations (rotating equipment and especially pumps) that are worth looking at in order to make some serious savings on energy costs.
This is why we warmly recommend that you start investing in magnetic, Non-Contact Drives (and save energy at the same time).
How may we help you?
There are many advantages to Non-Contact magnetic drives over ‘classic’ solutions.
A non-contact variable speed drive offers many benefits, including energy savings of up to 50%…
- Easy to install in three hours by removing the fixed coupling and replacing it with a magnetic coupling.
- No need for complicated cabling, additional filters (harmonic, sinus) compared to a VFD.
- ATEX certified. Easily applicable in explosive environments compared to an electronic VFD with ignition hazard.
- Can be located within ATEX safe zones, eliminating the need for long, expensive cables of 80 to 1,000 metres compared to a VFD.
- No motor wear (no motor bearing fluting, no motor winding insulation wear) due to harmonic pollution, increasing motor life up to two times.
- No impact on motor cooling compared to VFD, which requires an additional external motor fan to maintain a constant temperature.
- No cavities in the pump casing, impeller, pipework and throttle valve. Less cavitation in the piping system also means (much) less leakage.
- No shaft loading on motor and pump shaft due to unavoidable operating misalignment. So, motor and pump bearings last much longer.
And many, many more… But before we totally overwhelm you, please download the complete and practical white paper ‘A Clever, Reliable, and Proven Way to save on Industrial Energy Costs’
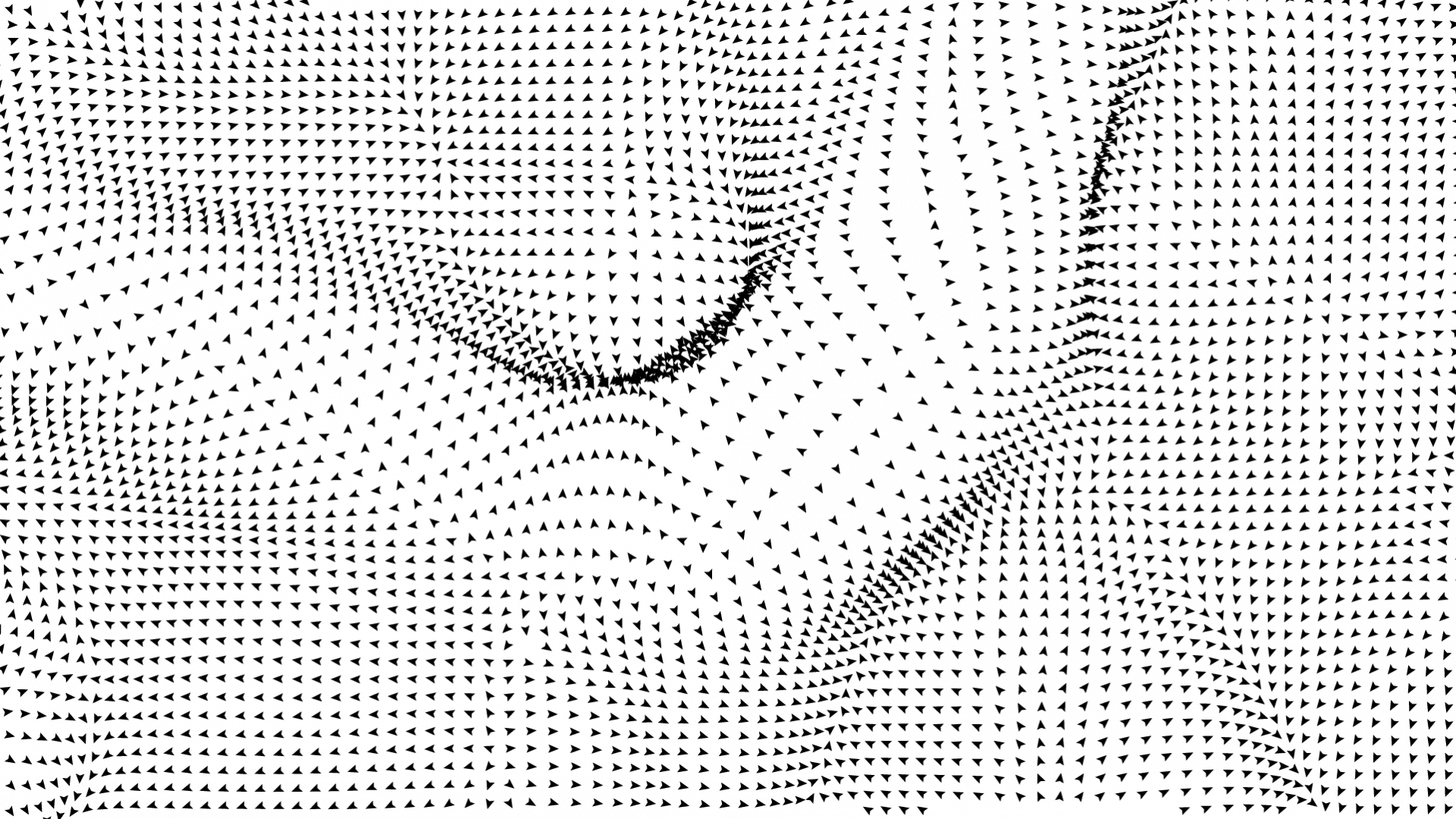
Whitepaper
Download
"*" indicates required fields
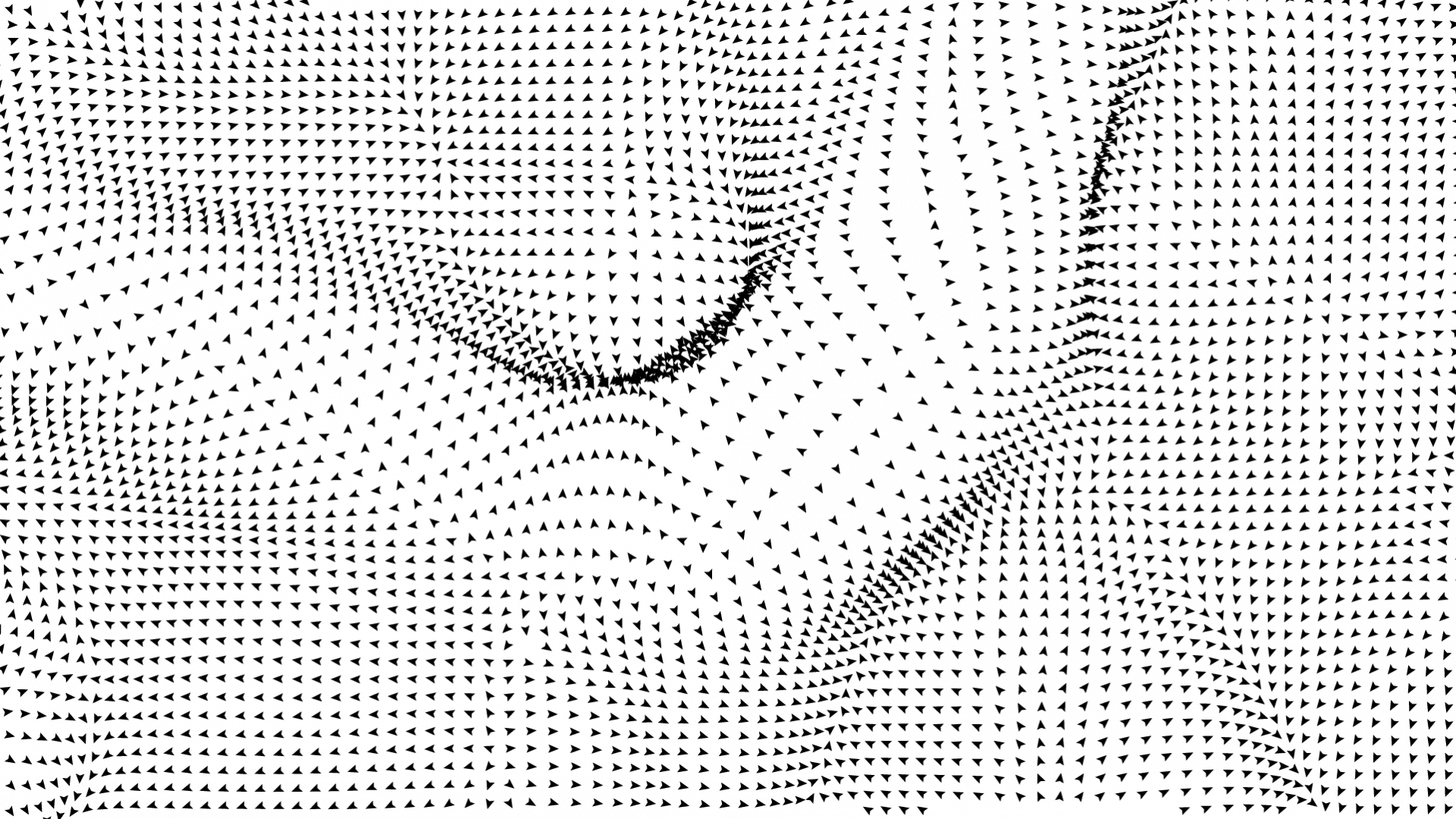